Autoclave Oven

In the world of scientific research and medical practices, ensuring the utmost sterility and safety is of paramount importance. One essential tool that plays a crucial role in achieving this goal is the autoclave oven. This specialized equipment is designed to sterilize a wide range of materials, from surgical instruments to laboratory glassware, by subjecting them to high-pressure steam and heat. With its ability to eradicate even the most resilient microorganisms, the autoclave oven is an indispensable asset in various industries, from healthcare to research institutions.
However, beyond its basic function, the autoclave oven offers a myriad of advanced features and capabilities that set it apart as a versatile and indispensable tool. In this comprehensive article, we will delve deep into the world of autoclave ovens, exploring their intricate workings, diverse applications, and the cutting-edge technologies that define their modern iterations. By the end of this journey, you will gain a profound understanding of the pivotal role autoclave ovens play in maintaining the highest standards of cleanliness and safety, as well as their indispensable place in modern scientific and medical practices.
The Evolution of Autoclave Ovens: A Historical Perspective

The concept of sterilization using steam and pressure is not a new one. In fact, the origins of autoclaving can be traced back to the early 19th century when French scientist Charles Chamberland developed the first autoclave, known as the autoclave à vapeur saturée, for use in Pasteur’s laboratory. This groundbreaking invention marked a significant milestone in the history of sterilization, as it provided a reliable and efficient method for eliminating microorganisms from a variety of materials.
Over the years, autoclave technology has undergone a remarkable evolution, driven by advancements in science and the increasing demands of various industries. From the early, cumbersome models that required constant manual monitoring to the sleek, computerized autoclave ovens of today, the journey has been one of constant innovation and refinement. Each generation of autoclave ovens has brought with it new features, enhanced capabilities, and improved efficiency, making them an indispensable tool in a wide range of applications.
The Early Days: Manual Autoclave Ovens
The early autoclave ovens were largely manual, requiring constant attention and supervision from operators. These devices consisted of a large metal chamber, often made of stainless steel, which was loaded with the materials to be sterilized. Once the chamber was sealed, the operator would manually control the heating elements and monitor the pressure and temperature gauges. This process was time-consuming and labor-intensive, often requiring hours of careful observation to ensure the sterilization cycle was completed successfully.
Despite their manual nature, these early autoclave ovens played a crucial role in the advancement of science and medicine. They were used extensively in research laboratories, hospitals, and even in the emerging field of biotechnology to sterilize a wide range of materials, from surgical instruments and glassware to cell cultures and biological samples. The ability to consistently produce sterile environments greatly enhanced the accuracy and reliability of scientific experiments and medical procedures.
The Rise of Semi-Automated Autoclaves
As technology advanced, so did the capabilities of autoclave ovens. The late 20th century saw the emergence of semi-automated autoclave ovens, which incorporated rudimentary electronic controls and timers. These innovations allowed for more precise control over the sterilization cycle, reducing the need for constant manual monitoring. The addition of timers enabled operators to set specific time intervals for different stages of the cycle, ensuring more consistent results.
Semi-automated autoclave ovens also introduced new features such as automatic pressure release valves and advanced monitoring systems. These innovations not only improved the safety of the sterilization process but also reduced the risk of operator error. With the ability to automatically release pressure and monitor critical parameters, these autoclave ovens provided a more reliable and efficient sterilization method, paving the way for further advancements in the field.
Modern Autoclave Ovens: The Cutting Edge of Sterilization Technology
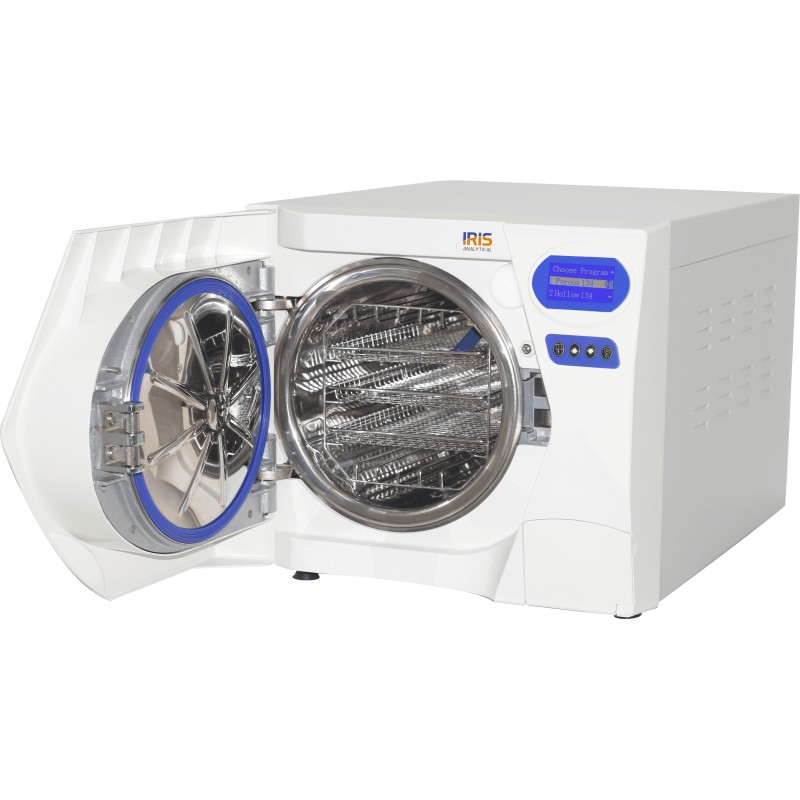
Today, autoclave ovens have evolved into sophisticated pieces of equipment, equipped with the latest technologies to ensure the most effective and efficient sterilization possible. Modern autoclave ovens are characterized by their advanced automation, precise control systems, and a range of innovative features that make them indispensable tools in a variety of industries.
Automated Control Systems
One of the most significant advancements in autoclave oven technology is the integration of fully automated control systems. These systems utilize advanced microprocessors and software to precisely control every aspect of the sterilization cycle, from the initial heating and pressurization to the final drying and cooling stages. Operators can input specific parameters for each cycle, ensuring consistent and repeatable results every time.
The automated control systems in modern autoclave ovens offer a host of advantages. They eliminate the need for constant manual monitoring, reducing the risk of human error and freeing up valuable time for other tasks. Additionally, these systems provide precise control over critical parameters such as temperature, pressure, and cycle duration, ensuring that every load is sterilized effectively and efficiently.
Advanced Monitoring and Data Logging
Another key feature of modern autoclave ovens is their advanced monitoring and data logging capabilities. These ovens are equipped with a range of sensors that continuously monitor critical parameters throughout the sterilization cycle. This real-time data is then logged and stored, providing a detailed record of each cycle’s performance. This information is invaluable for quality control, validation, and troubleshooting purposes.
By analyzing the data logged during each cycle, operators and quality control personnel can ensure that the autoclave oven is performing optimally and that the sterilization process is consistently effective. This level of monitoring and data logging is particularly important in industries where regulatory compliance and quality assurance are critical, such as pharmaceuticals, medical device manufacturing, and food processing.
Innovative Features for Enhanced Performance
Modern autoclave ovens are not only characterized by their advanced control systems and monitoring capabilities but also by a range of innovative features that enhance their performance and versatility. These features include:
- Advanced Chamber Designs: Modern autoclave ovens often feature advanced chamber designs, such as double-walled construction, which provides superior insulation and heat retention. This design ensures more efficient heating and cooling, reducing cycle times and energy consumption.
- Precise Temperature and Pressure Control: With highly accurate temperature and pressure sensors, modern autoclave ovens can maintain precise conditions throughout the sterilization cycle. This level of control ensures consistent and reliable results, even for the most demanding applications.
- Automatic Door Locking and Sealing: Advanced autoclave ovens are equipped with automatic door locking mechanisms that ensure a secure seal during the sterilization process. This feature not only enhances safety but also prevents contamination and ensures the integrity of the sterilization cycle.
- Programmable Drying Cycles: Many modern autoclave ovens offer programmable drying cycles, allowing operators to customize the drying process to suit specific load requirements. This feature is particularly useful for laboratories and research facilities that work with a wide range of materials, as it ensures optimal drying for each load.
Feature | Description |
---|---|
Chamber Size | Varies based on model, offering a range of capacities to accommodate different load sizes. |
Cycle Time | Varies, typically ranging from 30 minutes to several hours, depending on load and sterilization requirements. |
Temperature Range | 121°C to 134°C (250°F to 273°F) for standard sterilization cycles. |
Pressure Range | 15 psi to 30 psi, providing the necessary pressure for effective sterilization. |

Applications of Autoclave Ovens: Where Sterilization is Crucial
Autoclave ovens are indispensable tools in a wide range of industries and applications where sterilization is critical. Their ability to eliminate microorganisms and ensure the highest levels of cleanliness makes them an essential component in maintaining safety and reliability. Let’s explore some of the key industries and applications where autoclave ovens play a vital role.
Healthcare and Medical Facilities
Perhaps the most well-known application of autoclave ovens is in healthcare and medical facilities. Hospitals, clinics, and dental offices rely on autoclave ovens to sterilize a wide range of equipment and supplies, including surgical instruments, medical devices, and even textiles. By subjecting these items to high-pressure steam, autoclave ovens effectively eliminate bacteria, viruses, and other pathogens, ensuring that medical procedures are conducted in a safe and sterile environment.
In addition to sterilizing equipment, autoclave ovens are also used in healthcare facilities to treat infectious waste. By subjecting contaminated materials to high-temperature steam, autoclave ovens can render them safe for disposal, reducing the risk of disease transmission and environmental contamination.
Pharmaceutical and Biotechnology Industries
The pharmaceutical and biotechnology industries are heavily reliant on autoclave ovens for a variety of applications. From the sterilization of equipment and materials used in drug manufacturing to the preparation of cell cultures and biological samples for research, autoclave ovens play a critical role in maintaining the highest standards of cleanliness and safety.
In pharmaceutical manufacturing, autoclave ovens are used to sterilize a wide range of equipment, including vials, syringes, and other packaging materials. This ensures that the final drug products are free from any contaminants that could compromise their effectiveness or safety. In biotechnology research laboratories, autoclave ovens are essential for sterilizing cell culture media, reagents, and other sensitive materials, allowing scientists to conduct their experiments with the highest level of precision and accuracy.
Research Laboratories and Academic Institutions
Research laboratories and academic institutions are another key application area for autoclave ovens. These facilities rely on autoclave ovens to sterilize a wide range of equipment and materials used in scientific experiments, ensuring the accuracy and reliability of their research findings. From sterilizing glassware and laboratory equipment to preparing biological samples, autoclave ovens are an indispensable tool in the pursuit of scientific knowledge.
In addition to their role in sterilizing equipment and materials, autoclave ovens are also used in research laboratories for a variety of specialized applications. For example, autoclave ovens can be used to sterilize and prepare soil samples for microbiological studies, ensuring that the samples are free from any contaminants that could affect the experimental results. They are also used in the sterilization of plant tissues and seeds for agricultural research, helping scientists study the effects of various treatments and environmental conditions.
Food Processing and Packaging Industries
The food processing and packaging industries also benefit greatly from the use of autoclave ovens. These ovens are used to sterilize a wide range of food contact materials, including packaging, utensils, and even certain types of food products. By subjecting these materials to high-temperature steam, autoclave ovens eliminate bacteria and other microorganisms, ensuring that the final food products are safe for consumption and meet the highest standards of food safety regulations.
In addition to sterilizing food contact materials, autoclave ovens are also used in the processing of certain types of food products, particularly those that require high-temperature treatment to ensure their safety and shelf life. For example, autoclave ovens are used in the production of canned foods, where the high-temperature steam treatment helps to kill bacteria and prevent spoilage, ensuring that the canned goods remain safe and edible for an extended period of time.
The Science Behind Autoclave Ovens: How They Work
At the heart of every autoclave oven lies a complex set of scientific principles and processes that work together to achieve effective sterilization. Understanding the science behind autoclave ovens is crucial to appreciating their importance and the role they play in maintaining cleanliness and safety across various industries.
The Principles of Steam Sterilization
Autoclave ovens operate on the principle of steam sterilization, which is a highly effective method for eliminating microorganisms. Steam sterilization is based on the concept that microorganisms, including bacteria, viruses, and spores, are highly susceptible to the combination of high temperature and moisture. By subjecting materials to saturated steam at elevated temperatures and pressures, autoclave ovens can effectively kill or deactivate a wide range of microorganisms.
The effectiveness of steam sterilization lies in its ability to penetrate even the smallest crevices and reach all surfaces of the materials being sterilized. Unlike other sterilization methods, such as dry heat or chemical sterilization, steam can penetrate into porous materials and reach hidden areas where microorganisms may be present. This ensures that no area is left untreated, providing a thorough and reliable sterilization process.
The Sterilization Cycle: A Step-by-Step Process
The sterilization cycle in an autoclave oven is a carefully controlled and sequential process designed to ensure the complete elimination of microorganisms. While the specific steps and durations may vary depending on the model and application, the general sterilization cycle can be broken down into several key stages:
- Loading and Sealing: The process begins with loading the materials to be sterilized into the autoclave oven. Once the load is in place, the door is sealed to create an airtight environment.
- Pre-Vacuum (Optional): In some autoclave ovens, a pre-vacuum stage is employed to remove air from the chamber. This step helps to ensure that the steam can penetrate all areas of the load effectively.
- Heating and Pressurization: The autoclave oven is then heated, and pressure is increased to reach the desired sterilization conditions. This stage typically involves heating the chamber to a temperature of around 121°C (250°F) or higher and maintaining a pressure of 15-30 psi.
- Sterilization: Once the desired temperature and pressure are reached, the sterilization stage begins. During this stage, the load is exposed to the high-temperature steam for a specific duration, typically ranging from 30 minutes to several hours, depending on the load and sterilization requirements.
- Exhaust and Drying: After the sterilization stage is complete, the autoclave oven begins to exhaust the steam and reduce the pressure. This is followed by a drying stage, where residual moisture is removed from the load. The drying stage is crucial to prevent the growth of microorganisms during storage and transportation.
- Cooling and Unloading: Once the drying stage is complete, the autoclave oven begins to cool down. Once the chamber reaches a safe temperature, the door can be opened, and the sterilized load can be removed.
Autoclave Oven Validation: Ensuring Effective Sterilization

Given the critical role that autoclave ovens play in ensuring cleanliness and safety, it is essential to validate their performance and ensure that they are functioning effectively. Autoclave oven validation is a rigorous process that involves a series of tests and procedures to verify that the oven is capable of consistently achieving the desired sterilization conditions.
The Importance of Validation
Validation is crucial for several reasons. Firstly, it provides assurance that the autoclave oven is operating within its specified parameters and is capable of delivering the required sterilization conditions. This is particularly important in industries where regulatory compliance is critical, such as pharmaceuticals and medical device manufacturing.
Secondly, validation helps to identify any potential issues or deficiencies in the autoclave oven's performance. By conducting validation tests, operators can detect problems such as inaccurate temperature or pressure readings, inadequate steam penetration, or other issues that could compromise the sterilization process. Identifying and addressing these issues ensures that the autoclave oven remains reliable and effective over its lifetime.
Validation Procedures and Protocols
Autoclave oven validation typically involves a combination of routine monitoring, periodic testing, and comprehensive validation studies. Routine monitoring involves continuously monitoring critical parameters such as temperature, pressure, and cycle duration to ensure that the autoclave oven is performing within its specified limits.
Periodic testing is conducted at regular intervals to assess the autoclave oven's performance over time. These tests may involve using biological or chemical indicators, which are specially designed to provide a visual or colorimetric response when exposed to specific sterilization conditions. By placing these indicators within the autoclave oven during a sterilization cycle, operators can verify that the desired conditions have been achieved.
Comprehensive validation studies are conducted to provide a more in-depth assessment of the autoclave oven's performance. These studies typically involve a series of rigorous tests, including temperature mapping, pressure profiling, and cycle validation. Temperature mapping involves measuring the temperature at various points within the autoclave oven to ensure uniform heating. Pressure profiling involves monitoring the pressure throughout the cycle to ensure that the desired pressure conditions are consistently achieved. Cycle validation involves a detailed analysis of the entire sterilization cycle, from loading to unloading, to ensure that all stages are performed correctly and effectively.
Maintaining Autoclave Ovens: Ensuring Optimal Performance
To ensure that autoclave ovens continue to deliver effective sterilization over their lifetime, proper maintenance and care are essential. Regular maintenance not only helps to prolong the lifespan of the equipment but also ensures that it operates at its peak performance, providing consistent and reliable sterilization results.