The Ultimate Guide to Gas Dissolution

Gas dissolution is a critical process in various industries, from food and beverage production to wastewater treatment and pharmaceutical manufacturing. It involves the controlled introduction and distribution of gases into liquids, offering numerous benefits such as improved product quality, enhanced chemical reactions, and effective pollution control. In this ultimate guide, we delve into the intricacies of gas dissolution, exploring the techniques, equipment, and best practices to optimize this essential process.
Understanding Gas Dissolution
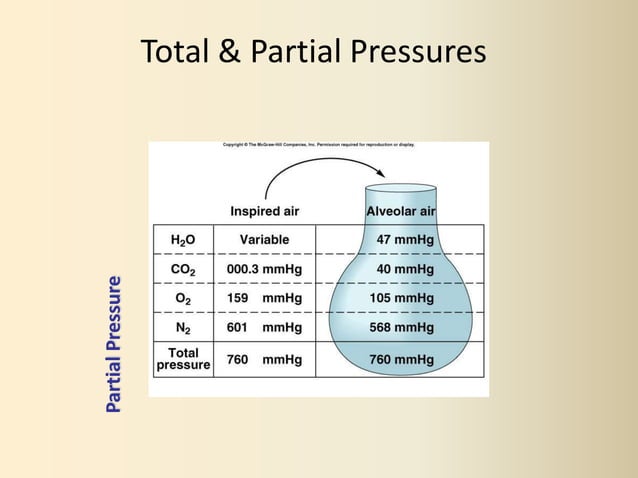
Gas dissolution, also known as gas absorption or mass transfer, is the process of transferring gases into liquids. It is a fundamental step in many industrial processes, as it enables the manipulation of chemical reactions, the extraction of valuable compounds, and the removal of pollutants. The efficiency of gas dissolution depends on several factors, including the nature of the gas and liquid, the contact time, and the surface area available for mass transfer.
One of the key challenges in gas dissolution is ensuring effective contact between the gas and liquid phases. This is where the right techniques and equipment come into play. By understanding the principles and best practices of gas dissolution, industries can optimize their processes, reduce costs, and improve overall efficiency.
Techniques for Gas Dissolution
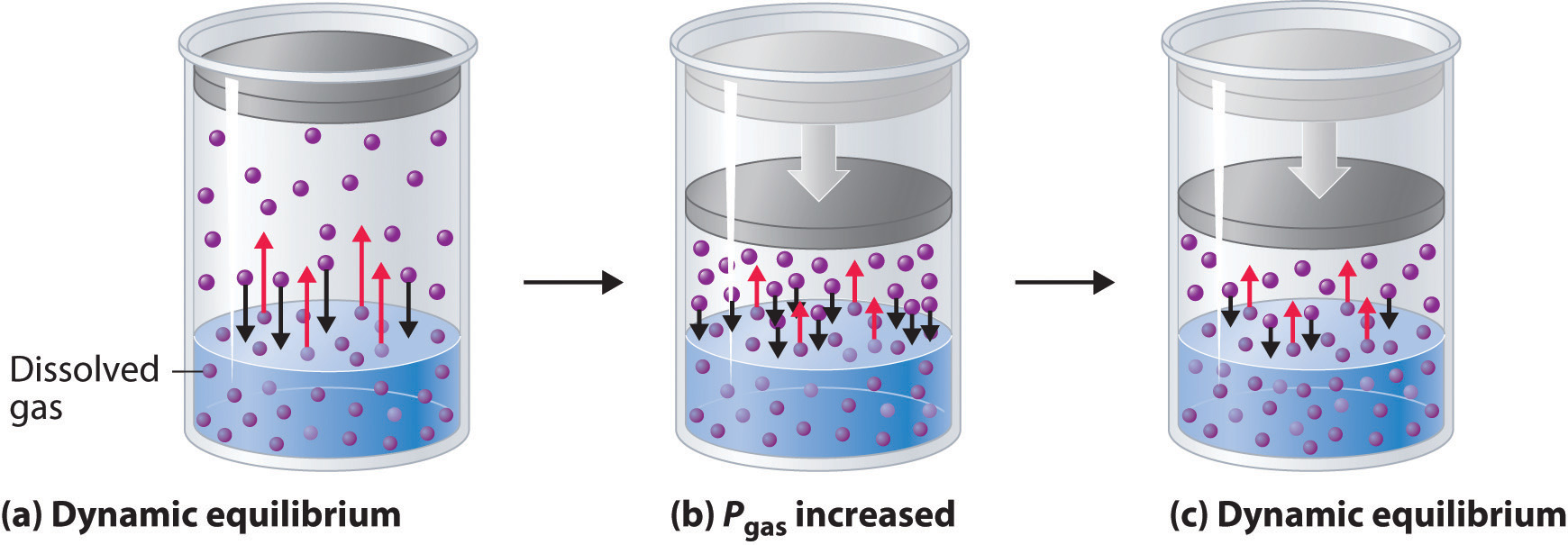
Spray Nozzle Systems
Spray nozzle systems are widely used in gas dissolution due to their simplicity and versatility. These systems atomize the liquid into fine droplets, increasing the surface area for gas-liquid contact. The droplets then mix with the gas, facilitating efficient mass transfer. Spray nozzles are particularly effective for applications where a large volume of gas needs to be dissolved quickly, such as in aeration processes.
Pros | Cons |
---|---|
High mass transfer efficiency | Potential for nozzle clogging |
Versatile for various liquids | Limited to specific gas pressures |
Easy to install and maintain | May require frequent cleaning |

Packed Columns
Packed columns are another popular technique for gas dissolution. These columns are filled with packing materials, such as Raschig rings or Pall rings, which provide a large surface area for gas-liquid contact. The gas and liquid are introduced into the column and flow counter-currently or co-currently, depending on the application. Packed columns are commonly used in processes where a high degree of gas-liquid contact is required, such as in chemical absorption and desorption.
Pros | Cons |
---|---|
Excellent mass transfer rates | Complex design and maintenance |
Suitable for viscous liquids | Limited to specific flow rates |
Efficient for high-volume applications | Potential for fouling and channeling |
Bubble Columns
Bubble columns, also known as bubble reactors, are simple yet effective devices for gas dissolution. They consist of a vertical column filled with liquid, into which gas is introduced through a sparger at the bottom. The gas forms bubbles that rise through the liquid, providing ample contact time for mass transfer. Bubble columns are commonly used in fermentation processes and wastewater treatment, where gas-liquid interactions are crucial.
Pros | Cons |
---|---|
Simple design and operation | Limited mass transfer efficiency |
Suitable for low-viscosity liquids | Bubble size variation can affect performance |
Low energy consumption | Potential for foaming and clogging |
Membrane Contactors
Membrane contactors offer a unique approach to gas dissolution, utilizing semi-permeable membranes to facilitate mass transfer. These contactors consist of a membrane module, typically made of hollow fiber or flat sheet membranes, through which the liquid flows. The gas is introduced on the opposite side of the membrane, and the selective permeability of the membrane allows for efficient gas dissolution. Membrane contactors are particularly useful for applications where gas solubility is low or when sensitive compounds are involved.
Pros | Cons |
---|---|
High gas dissolution rates | Sensitive to fouling and scaling |
Compact design and easy integration | Limited to specific gas pressures |
Suitable for sensitive compounds | High initial investment cost |
Equipment and Considerations
Selection of Gas Dissolution Equipment
Choosing the right equipment for gas dissolution depends on various factors, including the nature of the gas and liquid, the desired mass transfer rate, and the specific application. Here are some key considerations:
- Gas Solubility: Gases with high solubility, such as oxygen or carbon dioxide, may require less complex equipment compared to less soluble gases like nitrogen or hydrogen.
- Liquid Viscosity: Viscous liquids can pose challenges for certain techniques, such as packed columns, as they may hinder flow and mass transfer.
- Contact Time: The desired contact time between the gas and liquid should be considered when selecting equipment. Some techniques, like spray nozzles, offer shorter contact times, while others, like packed columns, provide longer residence times.
- Scalability: For large-scale operations, equipment that can be easily scaled up while maintaining efficiency is essential.
- Energy Efficiency: Certain techniques, like membrane contactors, offer energy-efficient solutions, which can be crucial for cost-effective operations.
Maintenance and Optimization
Regular maintenance is crucial to ensure the optimal performance of gas dissolution equipment. Clogging, fouling, and scaling can occur over time, affecting the efficiency of the process. Here are some maintenance tips:
- Implement a regular cleaning schedule to remove any accumulated solids or debris.
- Monitor equipment performance and conduct periodic performance tests to ensure mass transfer rates are within acceptable ranges.
- Replace worn-out components, such as spray nozzles or membrane modules, to maintain efficiency.
- Optimize gas and liquid flow rates to achieve the desired contact time and mass transfer.
- Consider using additives or coatings to reduce fouling and improve equipment longevity.
Applications and Benefits
Food and Beverage Industry
Gas dissolution plays a crucial role in the food and beverage industry, particularly in carbonation and oxygenation processes. Carbon dioxide is commonly used to carbonate soft drinks and beer, enhancing their flavor and effervescence. Oxygenation, on the other hand, is essential for maintaining the freshness and quality of beverages, as well as promoting the growth of beneficial microorganisms in fermentation processes.
Wastewater Treatment
In wastewater treatment, gas dissolution is utilized for various purposes. Oxygen is often introduced into activated sludge processes to promote the growth of microorganisms that break down organic pollutants. Nitrogen gas, on the other hand, is used in denitrification processes to remove excess nitrogen compounds, improving the overall water quality.
Pharmaceutical Manufacturing
The pharmaceutical industry relies on gas dissolution for processes such as drug synthesis and extraction. Gases like oxygen, nitrogen, and carbon dioxide are carefully controlled to optimize chemical reactions and prevent the degradation of sensitive compounds. Gas dissolution is also crucial in the production of aerosols and inhalation therapies.
Other Applications
Gas dissolution finds applications in a wide range of industries, including:
- Chemical processing for gas-liquid reactions and separation.
- Aquaculture for oxygenation and pH control.
- Biotechnology for cell culture and fermentation processes.
- Oil and gas industry for gas sweetening and gas injection.
Performance Analysis and Future Trends
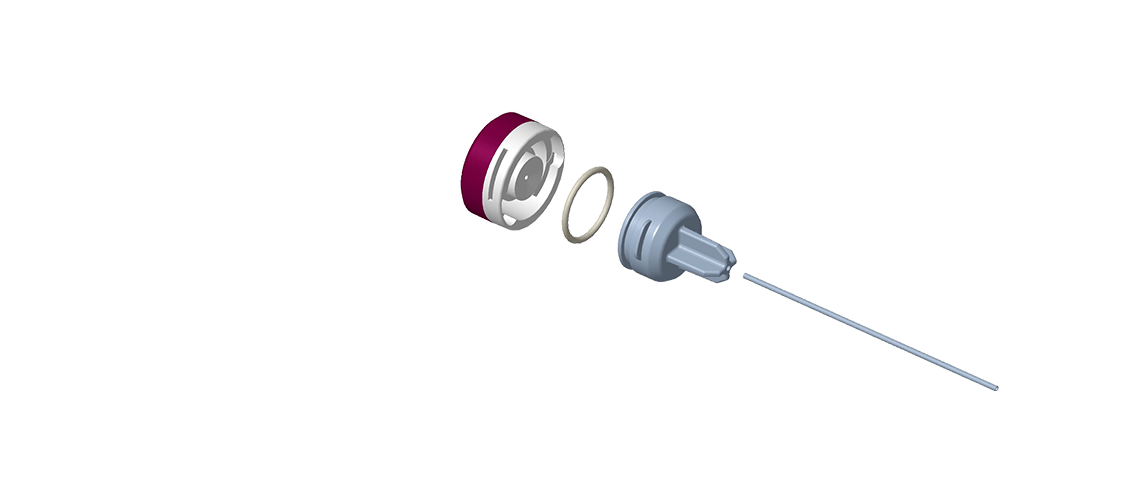
Performance Analysis
Analyzing the performance of gas dissolution processes is crucial to ensure efficiency and optimize operations. Several key parameters are typically considered:
- Mass Transfer Coefficient: This measures the rate of mass transfer between the gas and liquid phases. Higher mass transfer coefficients indicate more efficient dissolution.
- Gas Holdup: The volume fraction of gas in the liquid phase affects the overall gas-liquid contact and mass transfer.
- Bubble Size Distribution: In bubble columns, the size and distribution of bubbles can impact mass transfer efficiency and process stability.
- Pressure Drop: The pressure drop across equipment, such as packed columns, can affect the overall process efficiency and energy consumption.
Future Trends
The field of gas dissolution is constantly evolving, with ongoing research and development aimed at improving efficiency and addressing emerging challenges. Here are some future trends to watch:
- Advanced Membrane Technologies: Research is focused on developing more durable and selective membranes for gas dissolution, offering higher efficiency and longer lifetimes.
- Smart Monitoring and Control: The integration of advanced sensors and automation systems will enable real-time monitoring and control of gas dissolution processes, optimizing performance and reducing energy consumption.
- Microfluidic Systems: Microfluidic technologies offer the potential for precise and controlled gas-liquid interactions, particularly in lab-on-a-chip applications and micro-scale reactions.
- Hybrid Systems: Combining different gas dissolution techniques, such as membrane contactors with packed columns, may offer enhanced performance and flexibility for a wide range of applications.
Conclusion
Gas dissolution is a critical process in numerous industries, offering a wide range of benefits from improved product quality to effective pollution control. By understanding the techniques, equipment, and best practices, industries can optimize their gas dissolution processes, reduce costs, and enhance overall efficiency. As technology advances, the future of gas dissolution looks promising, with ongoing research and development paving the way for even more efficient and sustainable solutions.
What is the ideal gas-liquid ratio for optimal dissolution?
+The ideal gas-liquid ratio depends on various factors, including the nature of the gas and liquid, the desired mass transfer rate, and the specific application. In general, a higher gas-liquid ratio can enhance mass transfer efficiency, but it may also lead to increased energy consumption and potential foaming. It is essential to optimize the ratio based on the specific requirements of the process.
Can gas dissolution be applied to all types of liquids?
+Gas dissolution can be applied to a wide range of liquids, including water, organic solvents, and viscous liquids. However, the choice of technique and equipment may vary depending on the properties of the liquid. For instance, viscous liquids may require techniques with higher shear forces, such as spray nozzles or high-performance packed columns.
What are some common challenges in gas dissolution processes?
+Common challenges in gas dissolution processes include fouling, clogging, and scaling of equipment, which can affect mass transfer efficiency and process stability. Additionally, the selection of the right gas dissolution technique and equipment is crucial to ensure optimal performance and avoid issues such as limited mass transfer rates or excessive energy consumption.