Lockout Procedure
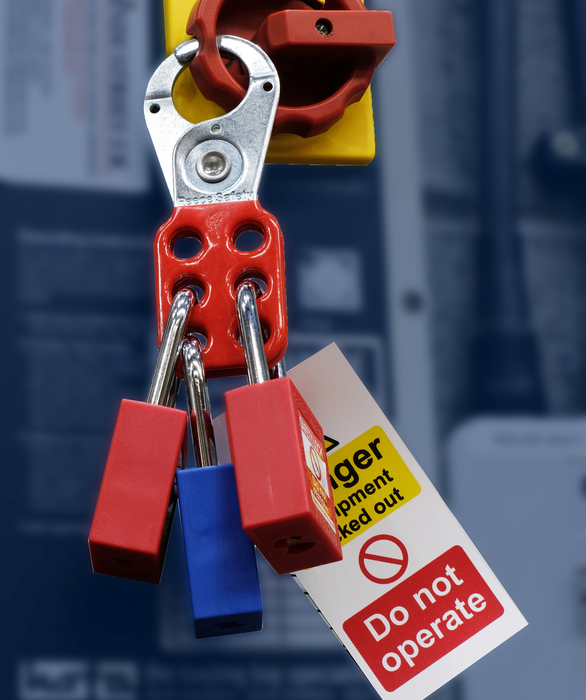
The lockout procedure is an essential safety protocol employed across various industries to prevent accidental start-up or release of hazardous energy during maintenance, repair, or servicing activities. This process ensures the safety of workers and equipment by de-energizing and securing machinery or systems to prevent unexpected reactivation. Proper lockout procedures are critical to avoiding injuries and fatalities in the workplace, making it a fundamental aspect of occupational health and safety.
The complexity of lockout procedures varies based on the type of equipment, potential energy sources, and the specific hazards associated with each. Understanding and implementing these procedures accurately is paramount to creating a safe working environment. This article will delve into the intricacies of lockout procedures, offering a comprehensive guide to ensure compliance and safety.
Understanding Lockout Procedures

Lockout procedures are standardized methods to control hazardous energy, often referred to as lockout/tagout (LOTO) protocols. These procedures involve a series of steps to achieve and maintain a state of zero energy, ensuring that machinery or equipment cannot be accidentally started or energized during maintenance or repair work.
The primary objective of lockout is to prevent the unexpected start-up of machinery or the release of stored energy, which could otherwise lead to serious injuries or fatalities. This process is critical in industries where heavy machinery, electrical systems, or potentially explosive substances are involved.
The Steps of a Typical Lockout Procedure
- Preparation and Planning: Before any maintenance work begins, a thorough assessment of the equipment and potential hazards is conducted. This step involves identifying all possible energy sources and developing a strategy to isolate and control them.
- Equipment Shutdown: The equipment is shut down in a safe and controlled manner, following the manufacturer’s instructions or established safety protocols. This step ensures that the equipment is in a stable state before proceeding.
- Isolating Energy Sources: All energy sources, including electrical, mechanical, hydraulic, pneumatic, and thermal, are isolated. This may involve switching off power supplies, blocking valves, releasing pressure, or disconnecting fuel lines.
- Lockout Application: Once the energy sources are isolated, specific lockout devices are applied to secure the energy-isolating devices. These devices can include padlocks, hasps, or specialized lockout equipment. Each authorized worker involved in the maintenance uses their personal lock, ensuring accountability.
- Verification of Isolation: It is crucial to verify that the equipment is indeed de-energized and secure. This step involves testing and inspecting the equipment to ensure that all energy sources are controlled and that the equipment cannot be accidentally activated.
- Maintenance or Repair Work: With the equipment safely locked out, maintenance or repair work can proceed without the risk of unexpected start-up. Workers can focus on their tasks knowing that the equipment is secure.
- Lockout Removal and Equipment Restart: Once the maintenance work is complete, the lockout devices are removed, and the equipment is slowly and carefully restarted. This step requires strict adherence to the manufacturer’s guidelines to ensure a safe restart.
Step | Description |
---|---|
1. Preparation and Planning | Assess equipment, identify hazards, and plan isolation strategy. |
2. Equipment Shutdown | Safely shut down equipment following established protocols. |
3. Isolating Energy Sources | Isolate all energy sources (electrical, mechanical, etc.) |
4. Lockout Application | Apply lockout devices to secure energy-isolating devices. |
5. Verification of Isolation | Test and inspect equipment to ensure complete de-energization. |
6. Maintenance Work | Conduct maintenance with assurance of equipment safety. |
7. Lockout Removal and Restart | Remove lockout devices and restart equipment safely. |

Importance of Lockout Procedures

Lockout procedures are vital for several reasons, primarily focused on occupational safety and compliance with legal regulations.
Safety Considerations
The primary purpose of lockout procedures is to prevent accidents and injuries. Without proper lockout, workers could be exposed to moving machinery, electrical arcs, explosive gases, or other hazardous conditions. These procedures ensure that equipment remains in a safe state during maintenance, protecting workers from harm.
For instance, in a manufacturing plant, a lockout procedure might involve shutting down a conveyor belt system, isolating electrical power, and applying locks to ensure that no one can accidentally restart the system while maintenance is underway. This simple yet effective procedure can prevent severe injuries or even fatalities.
Regulatory Compliance
Many countries have strict occupational health and safety regulations that mandate the use of lockout procedures. These regulations are designed to protect workers and ensure a safe work environment. Non-compliance can lead to severe penalties, including fines and legal repercussions.
In the United States, for example, the Occupational Safety and Health Administration (OSHA) has specific standards for lockout/tagout procedures. These standards outline the steps that employers must take to control hazardous energy and protect their workers. Failure to comply with these standards can result in citations and fines.
Reducing Downtime and Costs
While the primary focus is on safety, lockout procedures also play a role in minimizing downtime and associated costs. By following a standardized procedure, maintenance and repair work can be carried out efficiently and safely, reducing the risk of accidents that could lead to extended downtime.
Furthermore, proper lockout procedures can extend the lifespan of equipment by reducing the risk of damage caused by unexpected start-ups or the release of stored energy. This can lead to significant cost savings for businesses over time.
Challenges and Best Practices
Implementing lockout procedures can present challenges, especially in complex industrial settings. However, with proper training, standardization, and a culture of safety, these challenges can be effectively managed.
Common Challenges
- Complexity of Equipment: In industries with highly complex machinery, identifying and isolating all energy sources can be challenging. This complexity can lead to errors if not properly managed.
- Multiple Workers and Shifts: In a busy industrial environment, coordinating lockout procedures among multiple workers and shift changes can be difficult. Ensuring that all workers understand and adhere to the procedures is crucial.
- Lack of Standardization: Without clear and consistent lockout procedures, there is a higher risk of errors and non-compliance. Standardization ensures that all workers follow the same steps, reducing the margin for error.
Best Practices for Effective Lockout
- Comprehensive Training: All workers involved in maintenance or repair should receive thorough training on lockout procedures. This training should cover the identification of energy sources, the application of lockout devices, and the proper restart procedures.
- Clear and Visible Lockout Tags: Using clear and visible lockout tags can help communicate the status of equipment. These tags should provide information on the reason for lockout, the name of the authorized person, and the expected duration of the lockout.
- Regular Audits and Inspections: Conducting regular audits and inspections of lockout procedures can help identify areas for improvement and ensure that all workers are following the established protocols. These audits can also serve as training opportunities.
- Establish a Safety Culture: Creating a workplace culture that prioritizes safety and compliance is essential. This involves leadership commitment, worker engagement, and continuous improvement initiatives.
Future Trends and Innovations
As technology advances, the field of occupational safety is also evolving. Here are some trends and innovations that are shaping the future of lockout procedures.
Smart Lockout Devices
Traditional lockout devices, such as padlocks and hasps, are being enhanced with smart technologies. These smart devices can provide real-time data on the status of equipment, track maintenance history, and even send alerts if a lockout is compromised.
For example, some smart lockout devices use RFID technology to ensure that only authorized personnel can access and remove the lock. This adds an extra layer of security and control, reducing the risk of unauthorized equipment operation.
Digital Lockout Management Systems
Digital lockout management systems are being developed to streamline the lockout process and improve record-keeping. These systems can digitally manage lockout procedures, providing real-time visibility and control. They can also generate reports and track maintenance history, aiding in regulatory compliance.
Augmented Reality for Lockout Training
Augmented reality (AR) is being explored as a training tool for lockout procedures. AR can provide an immersive training experience, allowing workers to practice lockout procedures in a virtual environment before applying them in the real world. This can enhance understanding and reduce errors.
What are the key steps in a lockout procedure?
+The key steps include preparation and planning, equipment shutdown, isolating energy sources, lockout application, verification of isolation, maintenance work, and lockout removal and equipment restart.
Why are lockout procedures important?
+Lockout procedures are vital for preventing accidents and injuries, ensuring regulatory compliance, and minimizing downtime and associated costs.
How can we ensure effective lockout procedures in complex industrial settings?
+Comprehensive training, clear lockout tags, regular audits, and a strong safety culture are essential for effective lockout procedures in complex environments.
What innovations are shaping the future of lockout procedures?
+Innovations include smart lockout devices, digital lockout management systems, and augmented reality for training.