Personal Protective

The Evolution of Personal Protective Equipment (PPE): A Comprehensive Guide
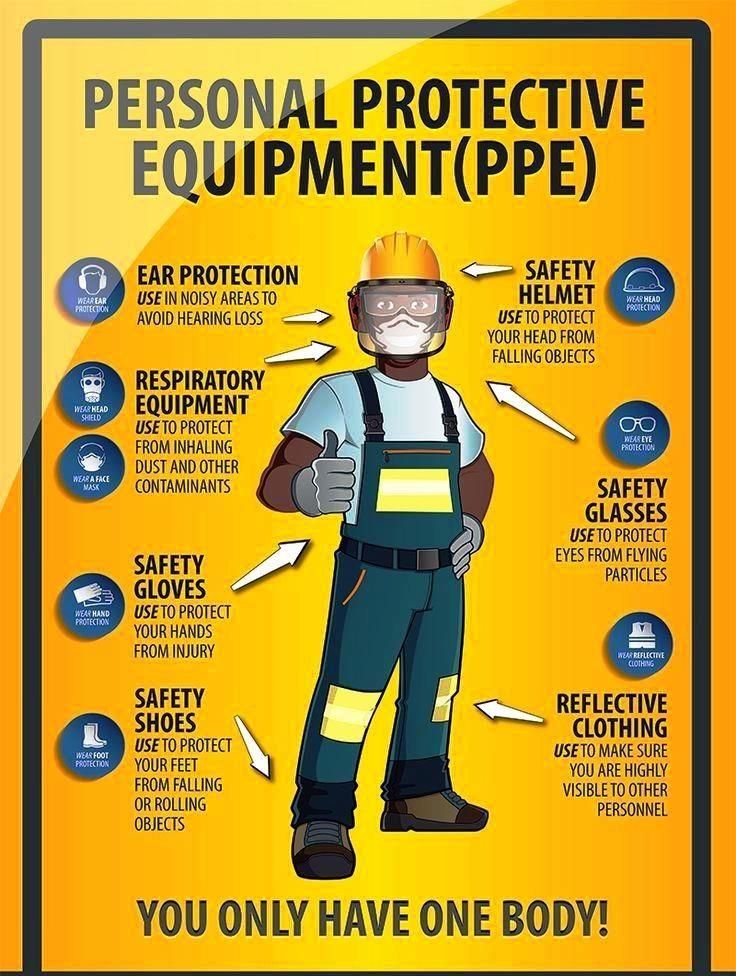
Personal protective equipment (PPE) has become an essential part of various industries, ensuring the safety and well-being of workers in hazardous environments. From construction sites to healthcare facilities, the right PPE can mean the difference between a minor incident and a serious injury. In this extensive guide, we delve into the world of PPE, exploring its evolution, the different types available, and the critical role it plays in protecting workers across diverse sectors.
The concept of personal protective equipment has evolved significantly over the years, adapting to the changing needs of industries and advancements in technology. What started as rudimentary forms of protection, such as leather aprons and metal helmets, has transformed into sophisticated, specialized gear designed to safeguard against a multitude of hazards.
Today, PPE is a multifaceted field, offering an array of products tailored to specific tasks and environments. This comprehensive guide aims to provide an in-depth understanding of PPE, its importance, and its applications, shedding light on how it has revolutionized worker safety and continues to do so.
The Historical Perspective: Evolution of PPE
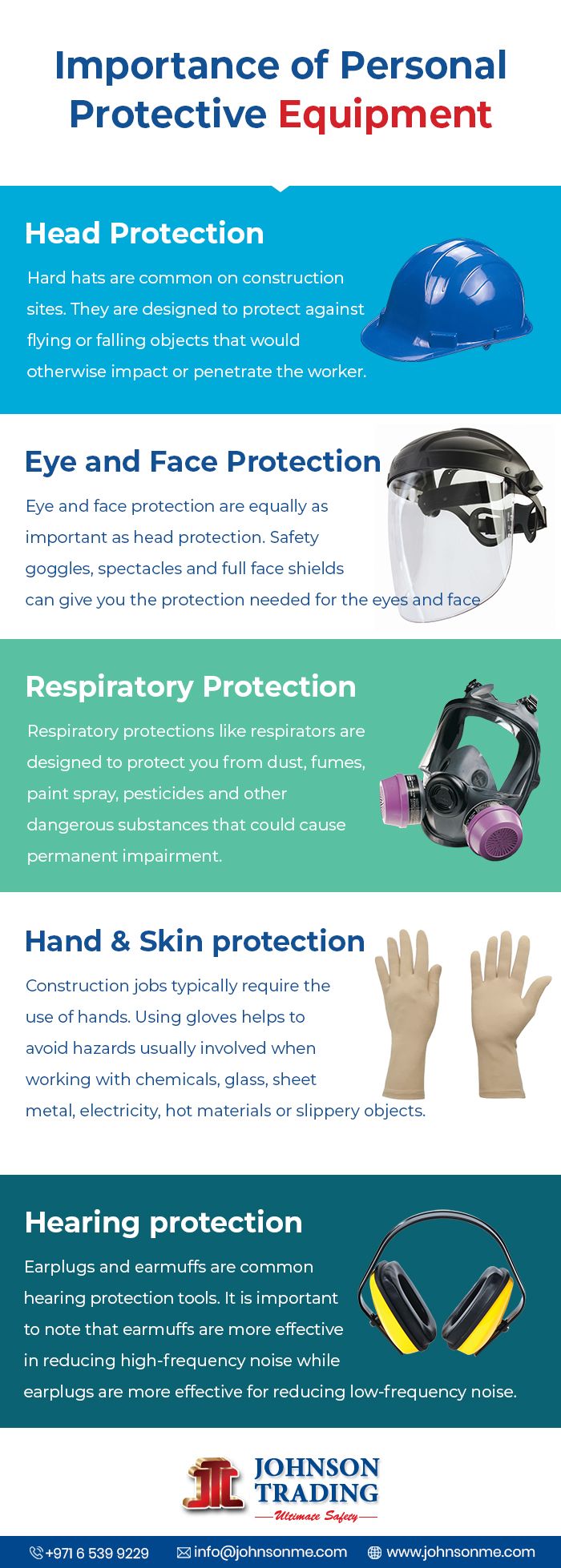
The history of personal protective equipment can be traced back to ancient civilizations, where early forms of protection were developed to safeguard workers from the dangers of their trades. For instance, the ancient Egyptians used simple leather gloves and aprons to protect their hands and bodies from sharp tools and hot materials during construction and crafting.
However, it wasn't until the Industrial Revolution that PPE began to take shape as we know it today. The rapid industrialization and the advent of machinery brought with them new hazards, leading to the development of more advanced protective gear. Hard hats, for example, were introduced in the early 20th century to protect workers from falling objects and head injuries, a common occurrence in the construction and mining industries.
The mid-20th century saw significant advancements in PPE technology. With the rise of the aerospace industry and the exploration of space, protective suits were designed to withstand extreme conditions, including high altitudes and low-oxygen environments. This period also marked the introduction of respirators, which played a crucial role in protecting workers from hazardous airborne particles and gases.
Key Milestones in PPE Development
- 1919: The first hard hat, known as the "Hard-Boiled Hat," was introduced by Bullard Company, a pioneer in the field of PPE. These hats were made from steamed canvas, glue, and black paint, offering a level of protection against head injuries.
- 1930s: The development of synthetic fibers, such as nylon and polyester, revolutionized PPE. These materials were lightweight, durable, and provided better protection against cuts and abrasions.
- 1940s: The introduction of rubber gloves and boots offered enhanced protection against chemicals and electrical hazards, becoming essential gear for workers in the chemical and electrical industries.
- 1970s: With the growing awareness of occupational health and safety, the Occupational Safety and Health Administration (OSHA) was established in the United States, leading to stricter regulations and standards for PPE.
- 1990s: Advancements in technology led to the development of smart PPE, integrating sensors and communication devices to enhance safety and provide real-time data on worker health and environmental conditions.
Understanding the Importance of PPE
Personal protective equipment serves as a crucial last line of defense, safeguarding workers from potential harm in hazardous environments. Its primary purpose is to reduce the risk of injury or illness by providing a barrier between the worker and the hazard. PPE is especially vital in industries where workers are exposed to physical, chemical, biological, or other types of hazards that could lead to severe injuries or long-term health issues.
The importance of PPE cannot be overstated, as it plays a pivotal role in:
- Preventing accidents and injuries: From simple cuts and bruises to more severe traumas, PPE can significantly reduce the risk of harm, often saving lives.
- Protecting against occupational hazards: Workers in various industries face unique hazards, such as chemical exposures, extreme temperatures, or biological pathogens. PPE is designed to mitigate these risks.
- Ensuring compliance with safety regulations: Many industries have strict guidelines and regulations regarding PPE usage. Compliance not only ensures worker safety but also avoids legal and financial repercussions.
- Promoting a culture of safety: When PPE is properly utilized and prioritized, it fosters a workplace culture that values safety and well-being, leading to increased productivity and morale.
Types of Personal Protective Equipment
Personal protective equipment encompasses a wide range of products designed to safeguard against various hazards. Here, we explore some of the most common types of PPE and their applications.
Head Protection
Head protection is crucial in industries where workers are at risk of head injuries, such as construction, mining, and manufacturing. Hard hats, the most common form of head protection, are designed to protect against impact, penetration, and electrical hazards. They come in various classes and types, depending on the nature of the work and the specific hazards present.
Type | Description |
---|---|
Type I | Designed to protect against impact to the top of the head, often used in construction and manufacturing. |
Type II | Provides protection against both top and lateral impacts, commonly used in logging, mining, and other industries with higher fall risks. |
Class E (Electrical) | Offers protection against electrical hazards, often used by electrical workers and linemen. |
Class G (General) | Provides a lower level of electrical protection compared to Class E, suitable for general construction and maintenance. |
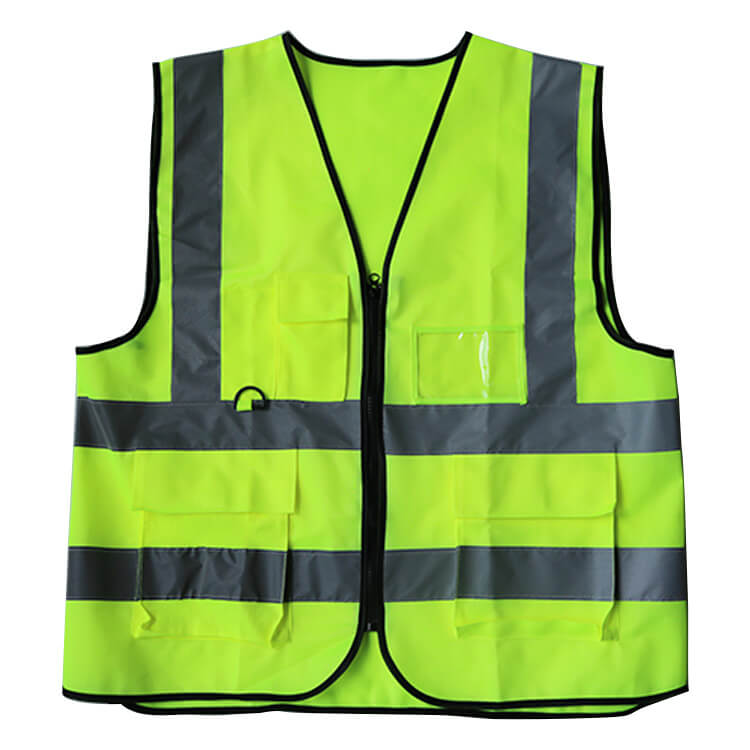
Eye and Face Protection
Eye and face protection is essential in environments where workers are exposed to flying debris, chemical splashes, or harmful radiation. Safety goggles, face shields, and welding helmets are some of the commonly used forms of eye and face protection.
- Safety goggles: These provide a tight seal around the eyes, protecting against impact, dust, and chemical splashes. They are often worn in laboratories, manufacturing, and construction sites.
- Face shields: Offering protection to the entire face, face shields are commonly used in healthcare settings to prevent exposure to bodily fluids and in industrial settings to protect against chemical splashes and flying debris.
- Welding helmets: Specialized helmets with dark filters, designed to protect the eyes and face from the intense light and sparks produced during welding.
Respiratory Protection
Respiratory protection is vital in environments with hazardous airborne substances, such as dust, fumes, gases, or biological agents. Respirators and breathing apparatuses are used to protect the respiratory system, ensuring workers can breathe safely in contaminated air.
- Half-face respirators: These cover the mouth and nose, providing protection against airborne particles and gases. They are often used in construction, agriculture, and chemical industries.
- Full-face respirators: Offering protection to the entire face, these respirators are commonly used in environments with higher levels of contamination or where both eye and respiratory protection are required.
- Powered Air-Purifying Respirators (PAPR): These systems use a battery-powered fan to draw air through a filter, providing clean air to the wearer. They are often used in healthcare settings and industrial environments with high levels of airborne contaminants.
Hand and Arm Protection
Hand and arm protection is crucial in industries where workers are at risk of cuts, punctures, burns, or chemical exposures. Gloves and arm sleeves are the primary forms of protection, offering varying levels of dexterity and protection depending on the specific task and hazard.
- Cut-resistant gloves: Made from materials like Kevlar or stainless steel, these gloves provide protection against sharp objects and are commonly used in manufacturing, waste management, and food processing industries.
- Chemical-resistant gloves: Constructed from materials like nitrile or neoprene, these gloves protect against chemical exposures, making them essential in chemical handling and laboratory settings.
- Heat-resistant gloves: Designed to protect against high temperatures, these gloves are often used in industries such as foundry work, glassblowing, and welding.
Foot and Leg Protection
Foot and leg protection is vital in industries where workers are at risk of foot injuries, such as construction, manufacturing, and agriculture. Safety boots and leg guards are designed to protect against impact, penetration, and chemical exposures.
- Safety boots: These boots often feature steel or composite toe caps to protect against impact and compression, making them suitable for construction and manufacturing environments.
- Metatarsal guards: Attached to the top of safety boots, these guards provide additional protection to the instep area, often required in industries with falling object hazards.
- Chemical-resistant boots: Made from materials like rubber or PVC, these boots protect against chemical spills and splashes, commonly used in chemical plants and laboratories.
The Future of Personal Protective Equipment

As technology continues to advance, the future of PPE looks promising, with ongoing innovations set to revolutionize worker safety. Here's a glimpse into what we can expect in the coming years.
Smart PPE
The integration of smart technologies into PPE is a growing trend, offering enhanced protection and real-time data monitoring. Smart PPE can include sensors that detect hazardous conditions, such as excessive heat, humidity, or the presence of toxic gases. These sensors can trigger alerts or automatically adjust the PPE to provide better protection.
3D Printing and Customization
3D printing technology is already being used to create customized PPE, ensuring a perfect fit for individual workers. This technology can be particularly beneficial in industries where off-the-shelf PPE may not provide adequate protection due to unique body shapes or sizes.
Advancements in Materials
Researchers are continuously developing new materials for PPE, focusing on improved protection, comfort, and durability. For instance, advancements in nanotechnology are leading to the creation of materials with enhanced barrier properties, providing better protection against chemical and biological hazards.
Wearable Technology
Wearable technology, such as smart watches and fitness trackers, is being integrated into PPE to monitor worker health and safety. These devices can track vital signs, detect fatigue, and even provide alerts if a worker is exposed to hazardous conditions, offering a proactive approach to worker safety.
Conclusion
Personal protective equipment has come a long way since its early beginnings, and its evolution continues to shape the way we approach worker safety. With ongoing advancements in technology and materials, PPE is becoming increasingly sophisticated, offering enhanced protection and comfort. As industries continue to prioritize worker safety, the importance of PPE will only grow, ensuring that workers can perform their jobs with confidence and peace of mind.
Stay tuned for further insights and updates on the world of PPE, as we continue to explore the latest innovations and their impact on worker safety and well-being.
How often should PPE be replaced or inspected for wear and tear?
+The frequency of replacement or inspection depends on the type of PPE and the level of wear and tear it experiences. As a general guideline, hard hats should be replaced every five years or sooner if they show signs of damage or deterioration. Respirators and other respiratory protection should be inspected and serviced regularly, following the manufacturer’s recommendations. Gloves, boots, and other protective gear should be inspected before each use and replaced if they show signs of damage or reduced effectiveness.
What are the legal requirements for PPE usage in the workplace?
+The legal requirements for PPE usage vary by country and industry. In the United States, the Occupational Safety and Health Administration (OSHA) sets standards for PPE usage in different industries. These standards outline the types of PPE required for specific tasks and the responsibilities of employers and employees in ensuring its proper use. It’s essential for employers to stay updated on these regulations and provide the necessary PPE to their workers.
How can workers ensure they are using PPE correctly?
+Proper training is crucial for ensuring workers use PPE correctly. Employers should provide comprehensive training on the selection, use, and maintenance of PPE. Workers should also conduct regular self-assessments, checking their PPE for fit, comfort, and functionality. If any issues are identified, workers should report them to their supervisors to ensure timely resolution.